Plastic extrusion for economical product fabrication
Plastic extrusion for economical product fabrication
Blog Article
A Comprehensive Overview to the Process and Benefits of Plastic Extrusion
In the large world of manufacturing, plastic extrusion arises as a necessary and highly effective process. Altering raw plastic right into continuous profiles, it caters to a plethora of markets with its impressive flexibility.
Comprehending the Essentials of Plastic Extrusion
While it may appear complex at very first glance, the process of plastic extrusion is fundamentally straightforward. The process starts with the feeding of plastic material, in the form of powders, pellets, or granules, into a heated barrel. The designed plastic is then cooled, strengthened, and reduced into desired sizes, completing the process.
The Technical Process of Plastic Extrusion Explained
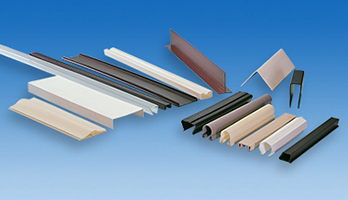
Sorts Of Plastic Suitable for Extrusion
The choice of the ideal kind of plastic is an essential facet of the extrusion process. Different plastics use distinct residential or commercial properties, making them a lot more matched to particular applications. Polyethylene, for example, is typically utilized because of its reduced price and very easy formability. It supplies superb resistance to chemicals and dampness, making it ideal for products like tubes and containers. Polypropylene is an additional preferred option due to its high melting factor and resistance to exhaustion. For even more robust applications, polystyrene and PVC (polyvinyl chloride) are typically selected for their strength and sturdiness. Although these are typical choices, the choice ultimately depends on the details needs of the item being created. So, recognizing these plastic kinds can substantially improve the extrusion process.
Contrasting Plastic Extrusion to Other Plastic Forming Approaches
Comprehending the sorts of plastic appropriate for extrusion leads the way for a more comprehensive discussion on exactly how plastic extrusion compares to other plastic developing methods. These consist of injection molding, blow molding, and thermoforming. Each approach has its distinct uses and advantages. Injection molding, for example, is outstanding for creating elaborate components, while impact molding is best for hollow objects like bottles. Thermoforming Read More Here excels at creating large view it now or shallow parts. Nonetheless, plastic extrusion is unmatched when it concerns developing continual profiles, such as seals, pipelines, and gaskets. It additionally allows for a constant cross-section along the size of the product. Therefore, the selection of method greatly depends on the end-product needs and specifications.
Trick Benefits of Plastic Extrusion in Production
In the world of production, plastic extrusion offers several considerable advantages. One significant benefit is the cost-effectiveness of the procedure, which makes it an economically attractive production method. Additionally, this method gives premium item versatility and enhanced production rate, consequently boosting overall manufacturing efficiency.
Affordable Production Approach
Plastic extrusion leaps to the center as an economical manufacturing approach in manufacturing. In addition, plastic extrusion requires less energy than traditional production techniques, adding to lower operational costs. Overall, the monetary advantages make plastic extrusion a very eye-catching alternative in the manufacturing industry.

Superior Item Flexibility
Past the cost-effectiveness of plastic extrusion, an additional substantial benefit in manufacturing lies in its premium item versatility. This makes plastic extrusion a suitable remedy for markets that require personalized plastic components, such as auto, building and construction, and product packaging. In essence, plastic extrusion's product versatility promotes technology while boosting functional effectiveness.
Enhanced Manufacturing Rate
A considerable benefit of plastic extrusion exists in its enhanced manufacturing speed. Few other production processes can match the rate of plastic extrusion. Furthermore, the capability to maintain constant high-speed manufacturing without giving up product high quality establishes plastic extrusion apart from other approaches.
Real-world Applications and Influences of Plastic Extrusion
In the world of manufacturing, the strategy of plastic extrusion holds extensive value. The economic benefit of plastic extrusion, mainly its economical and high-volume outcome, has actually reinvented production. The market is constantly making every effort for technologies in recyclable and biodegradable materials, suggesting a future where the benefits of plastic extrusion can be maintained without jeopardizing environmental sustainability.
Verdict
Finally, plastic extrusion is a view publisher site extremely reliable and reliable approach of transforming raw materials right into diverse items. It offers numerous benefits over various other plastic creating methods, including cost-effectiveness, high output, very little waste, and layout adaptability. Its effect is greatly felt in numerous sectors such as construction, automotive, and consumer goods, making it an essential procedure in today's production landscape.
Delving deeper right into the technological process of plastic extrusion, it starts with the option of the ideal plastic material. As soon as cooled, the plastic is cut right into the required lengths or wound onto reels if the product is a plastic film or sheet - plastic extrusion. Contrasting Plastic Extrusion to Other Plastic Forming Approaches
Understanding the types of plastic appropriate for extrusion leads the way for a wider discussion on exactly how plastic extrusion stacks up versus various other plastic developing methods. Few various other production processes can match the speed of plastic extrusion.
Report this page