Plastic extrusion for detailed profiles and custom designs
Plastic extrusion for detailed profiles and custom designs
Blog Article
Recognizing the Essentials and Applications of Plastic Extrusion in Modern Manufacturing
In the world of modern-day production, the technique of plastic extrusion plays an instrumental function - plastic extrusion. This elaborate process, involving the melting and shaping of plastic with specialized passes away, is leveraged across various sectors for the development of varied products. From auto parts to durable goods product packaging, the applications are huge, and the capacity for sustainability is equally outstanding. Deciphering the fundamentals of this procedure reveals truth adaptability and potential of plastic extrusion.
The Principles of Plastic Extrusion Refine
While it may show up complex, the basics of the plastic extrusion process are based on reasonably simple concepts. It is a manufacturing procedure where plastic is thawed and then shaped into a constant profile with a die. The raw plastic product, commonly in the kind of pellets, is fed into an extruder. Inside the extruder, the plastic goes through warm and stress, creating it to thaw. The liquified plastic is after that compelled through a shaped opening, known as a die, to form a long, constant product. The extruded product is cooled and after that cut to the preferred size. The plastic extrusion procedure is extensively used in different sectors because of its performance, convenience, and cost-effectiveness.
Various Sorts Of Plastic Extrusion Techniques
Structure upon the basic understanding of the plastic extrusion procedure, it is needed to discover the various techniques included in this production method. The 2 main strategies are profile extrusion and sheet extrusion. In account extrusion, plastic is melted and developed into a constant profile, frequently used to create pipes, rods, rails, and window structures. In comparison, sheet extrusion creates big, level sheets of plastic, which are usually more refined into products such as food packaging, shower drapes, and cars and truck components. Each technique needs specialized machinery and exact control over temperature level and pressure to make certain the plastic keeps its shape during cooling. Recognizing these strategies is essential to using plastic extrusion effectively in contemporary production.
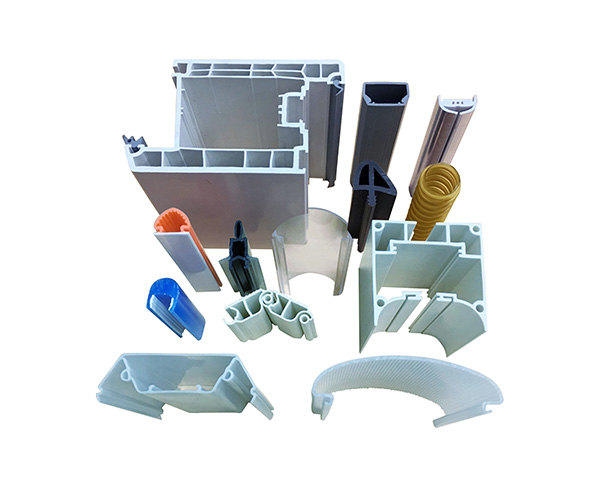
The Function of Plastic Extrusion in the Automotive Market
An overwhelming bulk of components in contemporary lorries are products of the plastic extrusion procedure. This process has transformed the automobile industry, changing it right into a much more effective, economical, and versatile manufacturing industry. Plastic extrusion is mainly utilized in the manufacturing of different auto parts such as bumpers, grills, door panels, and dashboard trim. The process supplies an uniform, constant outcome, allowing suppliers to generate high-volume get rid of fantastic accuracy and minimal waste. The lightness of the extruded plastic components adds to the general reduction in vehicle weight, enhancing fuel efficiency. In addition, the longevity and resistance of these components to warm, cold, and influence improve the long life of vehicles. Therefore, plastic extrusion plays an essential function in automotive manufacturing.

Applications of Plastic Extrusion in Customer Product Production
Beyond its considerable influence on the automobile sector, plastic extrusion shows just as effective in the realm of consumer goods manufacturing. The adaptability of plastic extrusion article source allows makers to make and produce complicated forms and sizes with high precision and effectiveness. The flexibility, adaptability, and cost-effectiveness of plastic extrusion make it a favored selection for numerous customer goods makers, contributing considerably to the sector's growth and development.
Ecological Influence and Sustainability in Plastic Extrusion
The pervasive usage of plastic extrusion in producing invites analysis of its environmental effects. As a procedure that regularly makes use of non-biodegradable materials, the environmental effect can be considerable. Energy intake, waste production, and carbon discharges are all worries. Market improvements are enhancing sustainability. Efficient equipment minimizes power usage, find out here now while waste administration systems reuse scrap plastic, reducing basic material demands. Additionally, the advancement of eco-friendly plastics supplies a much more eco-friendly alternative. Despite these improvements, better development is needed to mitigate the ecological impact of plastic extrusion. As culture leans towards sustainability, makers have to adapt to remain viable, stressing the value of constant research study and advancement in this area.
Conclusion
To conclude, plastic extrusion plays an important role in modern-day manufacturing, specifically in the auto and customer goods fields. Its versatility enables the production of a wide variety of parts with high precision. Furthermore, its possibility for recycling and advancement of biodegradable materials supplies an appealing method towards lasting practices, consequently addressing environmental worries. Understanding the basics of this procedure is key to enhancing its benefits and applications.

The plastic extrusion procedure right here is thoroughly made use of in numerous sectors due to its convenience, cost-effectiveness, and performance.
Building upon the basic understanding of the plastic extrusion procedure, it is needed to check out the different methods involved in this production technique. plastic extrusion. In contrast, sheet extrusion develops big, flat sheets of plastic, which are normally additional processed right into items such as food packaging, shower curtains, and car components.An overwhelming bulk of components in modern-day cars are products of the plastic extrusion procedure
Report this page